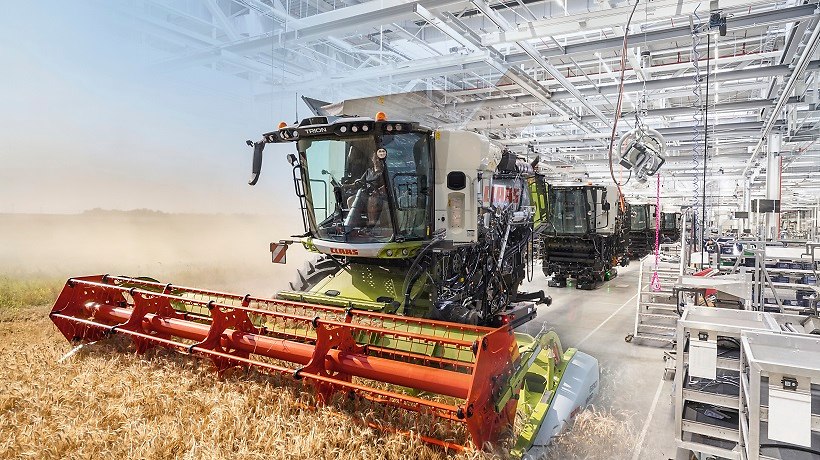
Open-heart surgery.
Ranging from 4.2 to 6.0 m high, the old assembly hall for combine harvesters was completely dismantled as part of the SynPro 2020 project – right in the middle of the main Harsewinkel plant.
A highly flexible and sustainable combine harvester production facility was built at the CLAAS headquarters in Harsewinkel as part of the SynPro 2020 project, with investments totalling €44 million. The previous two assembly lines were merged into one main line for the LEXION and TRION. Every day, our colleagues here build more than 20 combine harvesters for the world’s markets.
The original 15,000 m2 manufacturing hall was completely dismantled to make space for the world’s most advanced combine production facility. Included in this are shop floor management and the latest generation of IT infrastructure to ensure just-in-time parts logistics and assembly for the specific machines.
Over 40 different LEXION and TRION variants are built on the main assembly line, which is fed by sub-assembly lines on both sides for components and modules. Only smart and synchronised delivery of parts and their assembly is able to meet this challenge. That’s why the project was named SynPro. It stands for “Synchronised Production”. Automated guided vehicles or AGVs are used for every stage in assembling the prefabricated modules, from the first assembly point to commissioning on the test bench.
The “Once-in-a-Lifetime” ProjectAll videos at a glance
Excellence Harsewinkel.
Teaser.
Excellence Harsewinkel.
Clip 1.
Excellence Harsewinkel.
Clip 2.
Excellence Harsewinkel.
Clip 3.
Excellence Harsewinkel.
Clip 4.
Excellence Harsewinkel.
Clip 5.
Excellence Harsewinkel.
Clip 6.
Sometimes less is more: CLAAS is making even more customer wishes come true by transforming two separate assembly lines into one synchronised production facility. Together, the LEXION and TRION account for no fewer than 40 models and variants – and they are all assembled on a single line. From the 258 hp five-walker to the 790 hp hybrid combine. As wheeled machines, TERRA TRACs with crawler tracks and in the MONTANA version with undercarriage slope compensation.
Added to this is an endless array of custom equipment: Separation, cleaning, grain tank, straw chopper and distribution, slope conveyor, unloading auger tube, cab, CEMOS and much more. As many as 15,000 individual parts and components are then put together step by step to build precisely the right combine harvester for a wide range of applications and for CLAAS customers all over the world.
Explore LEXION diversity Explore TRION diversityThe silent and electric automatic guided vehicles carry the LEXION and TRION from the start of module assembly until they roll out of the factory gates. The load is not too heavy, initially at least. But it reaches five to ten tonnes later on. At wheel assembly, immediately before final roll-out, an AGV will carry up to 20 tonnes.
Digital connectivity keeps the AGVs moving automatically from station to station in complete sync. This is state-of-the-art technology and unrivalled in the agricultural machinery sector. Visitors can take in the numerous production steps at a glance from the new sky walk – the perfect place to embark on a factory tour.
In the first step, the shell module is primed and powder-coated and transported with the cleaning and steering axle to the main line on an AGV. Arriving there, the APS and APS SYNFLOW threshing units produced on the sub-assembly lines are already waiting on one side, while the rotor and walker modules for residual grain separation are on the other.
The engine unit is mounted together with the huge radiator packages once the threshing and separating elements and the front axle have all been installed. The radiators cool the engines reliably, even on hot and dusty days during the harvest season.
Entirely synchronised, the AGVs continue silently, carrying the gradually emerging LEXIONs and TRIONs. The grain tank and the cab are added at the next stations. They are both built almost exclusively in Harsewinkel – from the shell to the paintwork. This applies to the straw chopper module as well, which can be manufactured with ACTIVE SPREAD radial spreaders and chaff spreaders at the customer’s request.
Next up is assembly of the fuel storage tanks, the elevator and the tailings, the unloading auger tube and the slope conveyor. Finally, the combine harvesters receive all operating fluids up to the required filling level.
Now ready for operation, they are moved to one of six test stand cabins for commissioning. The side panels and remaining panelling can then be installed once this is complete. The LEXIONs and TRIONs are now ready for transport to the sales partner.
“Right-First-Time” applies to pre-assembly as well as to every module and component on the main line: Each LEXION and TRION should be built in such impeccable manufacturing quality that zero faults or defects are identified during commissioning and final quality control at the test bench.
Every single combine harvester is put through its paces after completion of basic assembly, so as soon all modules are operational and all the operating fluids have been added. Six test benches are then available: The electronics and electrics are tested step by step, in addition to the hydraulic functions and mechanics. GPS signal simulation is one of the highlights in this process. The steering system and telemetry need to operate trouble-free and with maximum precision from day one.
Once basic assembly is complete, the LEXION and TRION complete defined test cycles on six identical test benches.
This involves checking the mechanics, hydraulics, electrics and electronics, including wireless TELEMATICS data transmission.
The LEXION and TRION are not the only workplaces offering exceptional comfort. The combine production facility in Harsewinkel provides its employees with first-class, ergonomic working conditions for maximised motivation and concentration. After all, only satisfied employees build combine harvesters according to the most rigorous quality requirements.
Cranes and hydraulic lifting devices take care of the heaviest tasks, protecting the health of our employees. They can perform all tasks in a relaxed posture and without undue effort – from the first to the last combine harvester in their shift.
Skylights and LED illumination ensure steady and natural lighting conditions, irrespective of the weather outdoors. Light-coloured floors create a sense of hygiene and well-being. A new temperature management system and improved insulation keep things pleasantly warm in winter and refreshingly cool in summer. The new, six-tonne ventilation centre supplies the hall with around 80,000 m3 of fresh air per hour.
The low noise level also keeps our employees healthy and feeling relaxed. If you close your eyes, you will quickly forget you are right in the middle of a production facility for agricultural machinery. That’s how quietly our new assembly line operates.
New, welcoming common, break and wash rooms add to the well-being of our staff, along with the modern office workplaces. They are inviting places for everyone to relax and recharge their batteries during breaks, so they can then return to work with their concentration fully restored.
European market leader for combine harvesters and global leader for self-propelled forage harvesters – this success is no coincidence. It is the direct result of innovative spirit, product quality and professional service. And naturally down to the people who bring the CLAAS brand to life.
Developers who listen to farmers and contractors around the world and find creative and meaningful ways to put their wishes into practice. Production employees who use maximum precision to turn thousands of individual parts and components into bafflingly complex machines. Quality testers who never let things slide. Sales partners who provide expert advice. And service technicians who know the CLAAS machines like the backs of their hands.
Harsewinkel is also the birthplace and production site of the XERION. The large system tractor is virtually unrivalled thanks to its power and efficiency. Farmers and contractors in Western and Eastern Europe, North America, South America and Australia are thrilled by its versatility.
Technology leadership.
From the TRION 550 to the LEXION 8900 TERRA TRAC, CLAAS manufactures a wide range of modern and efficient combine harvesters in Harsewinkel.
Versatile, agile, strong.
The XERION is uniquely versatile on the global market thanks to an extremely resilient full frame, two steering axles and the rotating cab.
Efficient in all disciplines.
JAGUAR forage harvesters have been synonymous with output, chopped material quality, efficiency and low operating costs for 50 years.
Harsewinkel can boast a high level of vertical integration. The shells for many modules such as cleaning, primary and secondary separation as well as the grain tank are built and painted directly on site. This blends local know-how and skills with global competence.
CLAAS self-propelled harvesters are part of a world-wide competence and production network within the CLAAS Group. For example, the ground drives, variators and TERRA TRAC crawler units for the LEXION and TRION are developed and manufactured at CLAAS Industrietechnik in Paderborn. The steering and camera systems, telemetry modules and many other electronic components come from CLAAS E-Systems in Dissen. Combine headers and maize picker heads are manufactured in the Hungarian CLAAS factory in Törökszentmiklós.
Many Places. One Passion.TERRA TRAC crawler units, drives, gearboxes and variators are built by CLAAS Industrietechnik in Paderborn.
CLAAS E-Systems in Dissen delivers the steering and camera system, as well as the telemetry technology and other elements.
Töreksentmiklós in Hungary produces combine headers and maize pickers for the CLAAS Group.